Ndfeb hydrogen decrepitation.jpeg.
Jan 1, 2020 · Hydrogen decrepitation (HD) can be used as a direct reuse approach and effective method of recycling process to turn solid sintered magnets into a demagnetised powder for further processing.
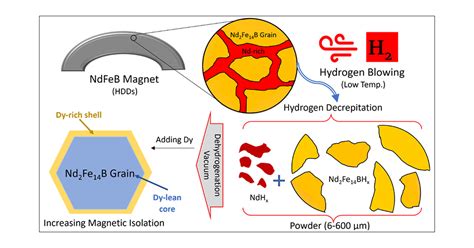
The application of hydrogen decrepitation (HD) as a process for recycling Nd-Fe-B sintered magnets was reported in [ 6 ], in which the essential role of hydrogen in the recycling process was demonstrated. The obtained magnetic properties of the recycled magnet were ( BH) max = 290 kJ/m 3 (±5 kJ/m 3 ), Br = 1240 mT (±50 mT) and jHc = …May 11, 2020 · Metallurgical simulation and evaluation of the resource efficiency of whole production processes are of key importance for sound environmental impact assessments. Exergy dissipation analysis is suitable to quantify the theoretical limits of a process and pinpoint hotspots for improvements along the value chain. Production of NdFeB permanent magnets is evaluated herein using a simulation-based ... In this paper, the hydrogen processing of scrap magnets has been demonstrated as an extraction method for NdFeB from automotive rotors for the first time, with the aim to …Mar 1, 2019 · The Hydrogen Decrepitation process (HD) is used as an alternative method of powder preparation in the manufacturing process of sintered Nd Fe B magnets [ 1]. During the HD process a NdFeB-type material is hydrogenated by gaseous hydrogen at atmospheric (or elevated) pressure at room (or elevated) temperature.
@article{osti_37277, title = {Hydrogen decrepitation of sintered NdFeB magnets}, author = {Stiller, C and Roth, S and Binner, A}, abstractNote = {The kinetics of the hydrogen absorption and desorption behavior of a NdFeB sintered magnet is studied. Hydrogenation at temperatures above 200 C is used to crumble the Nd-enriched phase. …Jun 27, 2014 · The scrap sintered Nd–Fe–B magnets were recycled as the raw materials for bonded magnets using the hydrogen decrepitation (HD) process. The HD powders have the lowest oxygen and hydrogen content by hydrogenation at 150 °C with 1 bar H2 pressure and dehydrogenation at 600 °C. The powders with the largest particle size (>380 μm) bear the best magnetic properties (B r = 110.59 emu/g, H cj ...
magnets. The thermal and mechanical impact of the hydrogen decrepitation process was assessed during hydrogen processing. For all forms of sintered NdFeB scrap the surface condition of the magnets is important as oxidation has been shown to inhibit the onset of the hydrogen decrepitation process. In this
Mar 1, 1985 · The hydrogen decrepitation (HD) process are studied in detail based on these results. The hydrogen absorption mechanism of Sm(CoFeCuZr) 7.6 alloy can be regarded as a hydrogen dissolution process without phase transformation. In addition, the existence of a large amount of fine grains in the SC has an adverse effect on the alignment, which can ... Hydrogen decrepitation (HD) of the sintered block was used to return the annealed material back into a powder [33]. During this step, the material reacts with hydrogen resulting in volume expansion of both the Nd-rich phase, at triple junctions and grain boundaries, and the Nd 2 Fe 14 B matrix phase [34]. This expansion leads to …In this paper it is demonstrated that hydrogen could play a vital role in this process. Fully dense, sintered NdFeB-type magnets have been subjected to the …A combination of hydrogen decrepitation (HD) and jet milling (JM) has been used to produce powder for the processing of permanent magnets. The procedure has proved to be very successful for both Nd-Fe-B (Neomax) alloys and the ND-Dy-Fe-Nb-B high coercivity alloys. The magnets produced by the HD/JM process showed excellent coercivities when …
The invention relates to a hydrogen decrepitation process for sintered Nd-Fe-B permanent magnets and belongs to the technical field of magnetic materials. The hydrogen decrepitation process includes melting metal materials, quickly solidifying the metal materials into cast pieces, activating the cast pieces under a certain condition, namely …
A combination of hydrogen decrepitation (HD) and jet milling (JM) has been used to produce powder for the processing of permanent magnets. ... The procedure has proved to be very successful for both NdFeB (Neomax) alloys and the NdDyFeNbB high coercivity alloys. The magnets produced by the HD/JM process showed excellent …
Electrolytic Hydrogen Decrepitation of NdFeB Magnets Under Ambient Conditions. V. Kaplan, Y. Feldman, …, I. Lubomirsky. Journal of Sustainable Metallurgy • Volume 8, Issue 3 • 1 September 2022. 1 citation; Scopus record. Article. 2D Pb-Halide Perovskites Can Self-Heal Photodamage Better than 3D Ones.The intrinsic magnetic coercivity (H ci) of Nd‐Fe‐B‐based permanent magnet material is profoundly affected by hydrogen absorbed during the hydrogen decrepitation (HD) process for producing anisotropic powders from bulk anisotropic hot‐deformed MAGNEQUENCH (MQ) magnets.Hydrogen (H) content and x‐ray diffraction …Hydrogen decrepitation process has been applied for the first time for the direct recycling of SmCo 5 magnets. Industrially produced sintered SmCo 5 magnets were decrepitated by hydrogen gas at a pressure of 1 bar to 9.5 bar at room temperature in a planetary rotating jar. After decrepitation, the starting sintered magnets were reduced to …Michihide Nakamura, Masashi Matsuura, Nobuki Tezuka, Satoshi Sugimoto, Yasuhiro Une, Hirokazu Kubo, Masato Sagawa; Preparation of ultrafine jet-milled powders for Nd-Fe-B sintered magnets using hydrogenation–disproportionation–desorption–recombination and hydrogen …(2020) Piotrowicz et al. Journal of Mining and Metallurgy, Section B: Metallurgy. Rare earth magnets based upon neodymium-iron-boron (NdFeB) are employed in many high tech applications, including hard disk drives (HDDs). The key elements in manufacturing NdFeB magnets are rare earth elements (REE...
0.5% -1%. Dysprosium (Dy) 0.8% -1.2%. The method of manufacture of Neodymium Iron Boron magnets is as follows: The Neodymium metal element is initially separated from refined Rare Earth oxides in an electrolytic furnace. The “Rare Earth” elements are lanthanoids (also called lanthanides) and the term arises from the uncommon oxide …The method combines hydrogen decrepitation (HD) disintegration of the initial magnet, powder sieving and the Press-Less Process (PLP), where hydride powder is sintered in a graphite mold. Coercivities up to 534 kA/m were obtained in porous samples based on powder size d < 100 µm. Adding a ball milling step resulted in full density …PDF (11 MB) Get e-Alerts SUBJECTS: Grain, Hydrogen, Hydrogenation, Magnetic properties, Organic reactions Abstract Regarding the restrictions recently imposed by China on the export of rare-earth elements (REEs), …Hydrogen decrepitation of Nd-Fe-B type magnet alloys is a two stage process. Firstly, the hydrogen reacts with the Nd-rich phase at or close to room …Jan 1, 2022 · The SC alloy is converted into a fine powder by hydrogen decrepitation and then jet-milling (JM) to produce a fine powder consisting almost entirely of single crystal particles of the Nd 2 Fe 14 B phase. This powder is then filled into fills molds and pressed while a magnetic field is applied to orient the individual particles. The compacted ... Jan 1, 2020 · Hydrogen decrepitation (HD) can be used as a direct reuse approach and effective method of recycling process to turn solid sintered magnets into a demagnetised powder for further processing. Hydrogen Decrepitation is a known process for breaking rare earth alloys such as NdFeB into powder, as described by Zakotnik et al. (“Hydrogen Decrepitation and Recycling of Sintered NdFeB-type Sintered Magnets”, Proceedings of 19 th International Workshop on Rare Earth Permanent Magnets & Their Applications; pp 289-295).
A combination of hydrogen decrepitation (HD) and jet milling (JM) has been used to produce powder for the processing of permanent magnets. The procedure has proved to be very successful for both Nd-Fe-B (Neomax) alloys and the ND-Dy-Fe-Nb-B high coercivity alloys. The magnets produced by the HD/JM process showed excellent coercivities when …Mar 14, 2016 · Hydrogen decrepitation (HD)/hydrogenation disproportionation desorption recombination (HDDR) is a process used in manufacturing REPM and carried out as pretreatment before green body sintering. During hydrogenation, the Nd-rich grain boundary phase in NdFeB magnets initially absorbs hydrogen forming Nd hydride: [ 49 ].
May 5, 2017 · The room temperature hydrogenation causes decrepitation of the material, where the Nd-rich material forms NdH 2.7 and the Nd 2 Fe 14 B matrix grains form an interstitial hydrogen solution. The material expands by ∼5% and because of its brittle nature and differential expansion, undergoes decrepitation [16]. Abstract. Some fully dense, sintered NdFeB-type magnets (employed in VCM disc drives) have been subjected to a recycling process using the hydrogen decrepitation (HD) process. After a brief milling treatment, the powder was aligned, pressed and re-sintered and this procedure was repeated four times with a progressive fall in the density …The initial step for manufacturing NdFeB plated permanent magnets in this unit process is NdFeB alloying and strip casting. NdFeB alloy is composed of 72% iron, 27% neodymium, and 1% boron from boron carbide (Sprecher et al., 2014). In order to stop free iron from forming, a small amount of iron formed between NdFeB crystals, the alloy is ...0.5% -1%. Dysprosium (Dy) 0.8% -1.2%. The method of manufacture of Neodymium Iron Boron magnets is as follows: The Neodymium metal element is initially separated from refined Rare Earth oxides in an electrolytic furnace. The “Rare Earth” elements are lanthanoids (also called lanthanides) and the term arises from the uncommon oxide …@article{osti_37277, title = {Hydrogen decrepitation of sintered NdFeB magnets}, author = {Stiller, C and Roth, S and Binner, A}, abstractNote = {The kinetics of the hydrogen absorption and desorption behavior of a NdFeB sintered magnet is studied. Hydrogenation at temperatures above 200 C is used to crumble the Nd-enriched phase. …Fig. 1. Illustration of the Hydrogen Decrepitation Press-Less Process (HD-PLP) recycling of anisotropic sintered NdFeB magnet. Passivated commercial N48M sintered magnets were used as starting material and hydrogen was applied to disintegrate the magnets inside a ball milling container. The hydride powder was both used directly …Hydrogen decrepitation process has been applied for the first time for the direct recycling of SmCo 5 magnets. Industrially produced sintered SmCo ... Nowadays, NdFeB magnets represent more than 90% of the REE permanent magnets production. But, SmCo magnets have much higher coercivity and better temperature resistance, and many experts expect ...Hydrogen Decrepitation (HD) has been used as an efficient and economical method in producing coarse NdFeB powder. This article studied the effects of hydrogen on the Nd-Dy-Fe-B magnets, such as HD ...
0.5% -1%. Dysprosium (Dy) 0.8% -1.2%. The method of manufacture of Neodymium Iron Boron magnets is as follows: The Neodymium metal element is initially separated from refined Rare Earth oxides in an electrolytic furnace. The “Rare Earth” elements are lanthanoids (also called lanthanides) and the term arises from the uncommon oxide …
Hydrogen decrepitation (HD) is an effective and environmentally friendly technique for recycling of neodymium-iron-boron (NdFeB) magnets. During the HD process, the NdFeB breaks down into a matrix phase (Nd2Fe14BHx) and RE-rich grain boundary phase. The grain boundary phase in the HD powder is <2 μm in size. Recycled NdFeB material has …
Jan 1, 2020 · Hydrogen decrepitation (HD) can be used as a direct reuse approach and effective method of recycling process to turn solid sintered magnets into a demagnetised powder for further processing. The behavior of hydrogen absorption and release in hydrogen decrepitation (HD) process of Nd-Fe-B alloys were investigated. The results reveal that the reactivity and the amount of hydrogen absorption in HD process are related to the surface activity of the alloy so that the fresh and active surface has a higher efficiency. The presence of Nd-rich phase at the …Keywords: Finite difference method; Kinetics; Hydrogen decrepitation; NdFeB alloys; Diffusion 1. Introduction Sv (V ) expansion due to decrepitation results in a five orders of magnitude higher rate of hydrogen diffusion into The most popular recent application of hydrogen in the Nd–Fe–B alloy than into a theoretical bulk sample of that ...The scrap sintered Nd–Fe–B magnets were recycled as the raw materials for bonded magnets using the hydrogen decrepitation (HD) process. The HD powders have the lowest oxygen and hydrogen content by hydrogenation at 150 °C with 1 bar H2 pressure and dehydrogenation at 600 °C. The powders with the largest particle size (>380 μm) …Another example of the coercivity recovery in crushed NdFeB-type sintered magnets was made by adding the DyF 3 salt [8]. Furthermore, the production of anisotropic RE–Fe–B–Cu powders have also been produced by hydrogen decrepitation of hot deformed ingots [9] followed by degassing.Sadly, one of the most common RE magnets, NdFeB, is produced as powder by strip casting and jet milling or by hydrogen decrepitation process, both of which yield irregular/angular powders. Such irregular powders exhibit low flowability making them unfit for most advanced manufacturing techniques. This work presents the use of an induction ...Hydrogen decrepitation as a highly efficient and excellent crushing method is widely used in the preparation of NdFeB magnets. ... Expand. 1. Save. The processing and characterisation of recycled NdFeB based magnets. S. Adrwish. Materials Science, Engineering. 2013; The scrap magnets were turned into a powder using the HD process. …The influence of the alloy granulation grade, temperature and surface oxidation on the kinetics and the course of the fracture processes during the hydrogenation of Nd16−xDyxFe76B8 (x=0–3) alloy was studied. The average particle sizes of the alloy were 1 mm, 5 mm and 3 cm and the temperature range between 20 and 200 °C. Pre-oxidation …Jan 1, 1991 · The subject of this paper is method (4) together with other aspects of the use of hydrogen in the processing of NdFeB-type magnets. 2. The hydrogen decrepitation process The manufacture of rare earth-transition metal magnets by the HD route was first proposed in a 1978 patent by Harris et al. [7]. hydrogen uptake (2043.76 μmol∙g-1) was received for conditions 4 bar and room temperature, while the lowest (925.27 μmol∙g -1 ) for 1 bar at 400 0 C (Figure 4). At room temperature (29
In this paper it is demonstrated that hydrogen could play a vital role in this process. Fully dense sintered NdFeB-type magnets have been subjected to the …The obtained strips were pulverized and further milled into ∼5 μm powder using hydrogen decrepitation and jet milling, respectively. These powders were pressed in a magnetic field of 1.8 T under a pressure of 8.0 MPa. Afterward, the green compacts were sintered at 1070°C for 3 h in vacuum, cooled by Ar quenching. ... NdFeB sintered …An effective and complete processing route for the recycling of sintered Nd-Fe-B scrap magnets was proposed. Sintered Nd-Fe-B magnets were subjected to the Hydrogen Decrepitation (HD) process at various temperatures in the range of 50–300 °C, at two different pressures, 50 kPa and 200 kPa, followed by vacuum dehydrogenation in …May 8, 2023 · An effective and complete processing route for the recycling of sintered Nd-Fe-B scrap magnets was proposed. Sintered Nd-Fe-B magnets were subjected to the Hydrogen Decrepitation (HD) process at ... Instagram:https://instagram. z40integratedi 75nmac woodesjfglis So exposure at LOW temperature to hydrogen leads the NdFeB pieces to react via intergranular fracturation (decrepitation), the mass of Nd2Fe14B grains forminfg a metal hydride with max ... wild pitch sports bar and grill fort worth photosfx2 As noted above, the calculated Gibbs energy of reactions of individual REE with atomic hydrogen (Table 1) is strongly negative, thereby predictive of rapid chemical decrepitation of the two-phase Nd-magnet within the temperature range of interest. These reactions can be expected to take place immediately … See moreMay 5, 2023 · The first is the hydrogen decrepitation (HD) process, which is already used in the primary production of NdFeB magnets to convert the alloy into powder form before further comminution. 46 The second process, named HDDR, which consists of two different steps, namely hydrogenation–disproportionation (HD) and desorption–recombination (DR), was ... sunny health and fitness NdFeB ingot exposed to hydrogen atmosphere due to the changes of hydride lattice parameters cracks. The process called HDDR (Hydrogenation - …We ascribe the volume expansion during ATF aging to the incorporation of hydrogen dissociated from the organic liquid ATF into the melt-spun NdFeB powder. Hydrogen is known to diffuse into the Nd2Fe14B crystal structure [2–4] and occupy interstitial sites to form the isomorphic hydride Nd2Fe14BHx with up to x=5 H per formula …